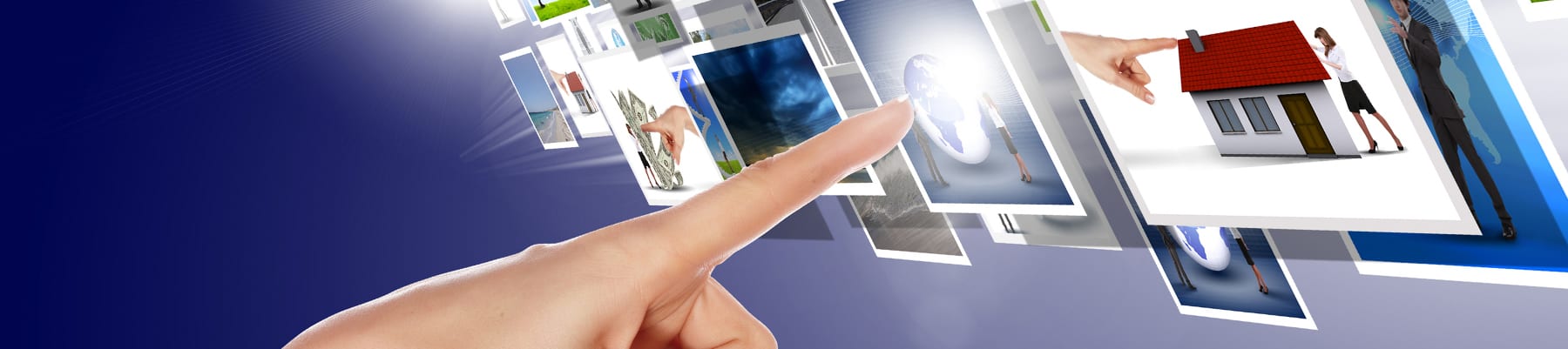
Resource Library
Technical Articles
In addition to offering superior lapping, polishing and machining of components made of high-purity silicon carbide and other advanced ceramics, we have information that could be useful as you make decisions about your design and requirements.
- Surface Roughness Considerations in Advanced Ceramics Manufacturing
As seen in Aerospace Manufacturing & Design magazine - Diamond Wheel Grinding 101
As seen in Ceramic Industry magazine
Literature & Ads
Learn more about our expertise and capabilities.
- Your One-Stop Shop
As seen in Ceramics Industry magazine - Take a Closer Look at Our Precision Machining Capabilities Ad
- PremaTech Advanced Ceramics Capabilities Brochure
Case Studies
Learn how PremaTech has helped customers in a wide range of industries improve efficiency, quality, and profitability. Adding measurable value to the companies we serve has made us a market leader.
Semiconductor Manufacturer Case Study
Full-Scale Involvement with Semiconductor Manufacturer Improves Product Quality & Assembly Yield
The Challenge
A manufacturer needed 10 different tapered ceramic components- the smallest parts used in the product. A previous supplier had been providing parts of inconsistent quality, and the customer asked PremaTech to produce and deliver superior ceramic components that the specifications required.
The Solutions
A team of PremaTech engineers defined critical dimensions for success in the manufacturing process, designed a fixture to keep the metalized surface centered while grinding the taper and met with the metalizing vendor to discuss important surface features. Those collaborative efforts led the vendor to recommend a nickel chrome coating instead of nickel for achieving desired resistivity. PremaTech engineers also worked collectively to determine an optimal adhesive thickness down to 0.0005″.
Two months later, PremaTech delivered 20 ceramic parts for First Article Inspection (FAI). The customer approved the FAI shipment and proceeded to order 700 parts. PremaTech also codified in-process steps, providing the customer with documented evidence of our standard quality control procedures.
The Benefits
By working with PremaTech, the manufacturer is experiencing an assembly yield in the 95% range, compared to an average of 50% with the previous supplier. This 45% gain is allowing the customer to enhance profitability and on-time delivery.
PremaTech has continued working with the customer to achieve additional process improvements.
Electronics Equipment Manufacturer Case Study
Technical Expertise & Responsiveness Excite Electronics Equipment Manufacturer
The Challenge
A major defense contractor approached PremaTech for assistance with the production of protective closures for electronics equipment. The customer developed a proprietary advanced ceramic material and needed help fabricating a prototype, as well as with production.
The Solutions
PremaTech machined Modulus of Rupture (MOR) bars to support material testing. PremaTech also took the customer’s extremely rough blanks and precision-ground the inner and outer 3-D surfaces to the stringent specifications developed by the U.S. Department of Defense’s prime contractor, providing large quantities of prototype parts during product development.
After the customer approved the prototypes, PremaTech ramped up to full production, providing exceptional product quality, and outstanding flexibility and responsiveness with regard to order turnaround times and quantities requested by the customer.
Finally, to the customer’s extreme satisfaction, PremaTech performed 3-D inspections on the component’s CAD-designed surface. Those tests yielded 100% compliance with quality requirements.
The Benefits
PremaTech’s ability to meet the customer’s stringent specifications, conduct prototype testing and engage efficiently in R&D activities has given the customer a reliable strategic partner that can work with them at every stage of development and production.
Based on 3-D inspection results, the customer trusts PremaTech implicitly to manufacture components of such high quality that the customer has eliminated acceptance testing, which has accelerated the customer’s order turnaround times.
Analytical Instruments Case Study
PremaTech Separates Itself from Competitors Through Work with Analytical Instruments Manufacturer
The Challenge
A publicly traded manufacturer of analytical instruments approached PremaTech Advanced Ceramics about some critical fluid handling components from Zirconia for use in a next generation analytical device.
The Solutions
A team of PremaTech engineers studied the customer’s specifications and recommended several types of zirconia that could work for the particular application. PremaTech then fabricated prototype parts from each grade of material.
After the customer selected the material, PremaTech worked closely with the customer’s engineers to optimize several critical features and dimensions. This collaboration led PremaTech to fabricate several design variations that maximized manufacturability and performance. The customer proceeded to finalize the design, allowing PremaTech to transition to volume production for one of the components.
The Benefits
With PremaTech’s help, the customer was able to fill orders successfully for its next-generation analytical device, and first-year shipments have exceeded the customer’s forecast significantly.
As PremaTech supports the customer’s volume production requirements for one of the components, it is conducting R&D related to the other component.
PremaTech’s capacity to support R&D and production simultaneously exemplifies the company’s ability to give customers a high degree of expertise and outstanding value at all stages of the product life cycle.